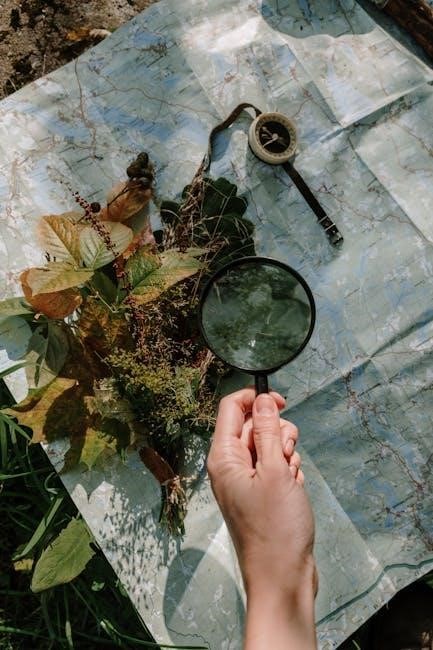
Guide bearings are essential mechanical components designed to control and direct motion between moving parts. They ensure precise alignment‚ reduce friction‚ and prevent wear in various industrial applications. Available in linear‚ spherical‚ and cylindrical types‚ these bearings are crucial for maintaining operational efficiency and stability in machinery. Their versatility makes them indispensable across industries‚ from aerospace to automotive‚ ensuring smooth and consistent performance. Proper installation and maintenance are key to their longevity and functionality.
1.1 Definition and Purpose
A guide bearing is a mechanical component designed to guide or control the motion of moving parts within a machine or system. Its primary function is to enable smooth‚ precise movement while maintaining proper alignment and reducing friction. Guide bearings are used to absorb forces‚ such as radial or axial loads‚ and prevent wear on adjacent components. They are essential for ensuring the proper functioning of machinery by providing a stable and consistent operational environment. Available in various designs‚ including linear‚ spherical‚ and cylindrical types‚ guide bearings cater to different industrial needs. Their purpose is to enhance the efficiency‚ accuracy‚ and longevity of equipment by minimizing mechanical stress and ensuring optimal performance. Proper installation and maintenance are critical to their effectiveness‚ as they directly impact the overall functionality of the machinery they support.
1.2 Importance in Machinery
Guide bearings play a critical role in machinery by preventing wear and tear on moving components. They ensure proper alignment and smooth operation‚ which is vital for maintaining efficiency and reducing downtime. By absorbing radial and axial loads‚ guide bearings protect machinery from structural stress‚ thereby extending its operational lifespan. Their ability to minimize friction and ensure precise movement is essential for maintaining the accuracy and reliability of mechanical systems. In industries where heavy machinery is prevalent‚ guide bearings are indispensable for handling high loads and ensuring continuous production. Their durability and ability to function under harsh conditions make them a cornerstone of modern machinery design. Without guide bearings‚ many industrial processes would suffer from frequent breakdowns and reduced performance‚ highlighting their importance in maintaining operational integrity and productivity.
Types of Guide Bearings
Guide bearings are classified into linear‚ spherical‚ and cylindrical types‚ each designed for specific applications. Linear bearings facilitate motion in straight lines‚ while spherical bearings handle multi-directional movement. Cylindrical bearings offer high load capacity and precision‚ making them ideal for heavy machinery. These types cater to diverse industrial needs‚ ensuring efficient and smooth operation in various mechanical systems.
2.1 Linear Guide Bearings
Linear guide bearings are designed to facilitate smooth motion in straight lines‚ ensuring precise alignment and minimal friction. They consist of a rail and a carriage or slider‚ which glides along the rail. These bearings are commonly used in applications requiring high accuracy‚ such as CNC machines‚ robotic arms‚ and precision instrumentation. Their robust design allows them to handle heavy loads while maintaining consistent performance. Linear guide bearings are available in various materials‚ including steel and ceramic‚ each offering unique advantages like durability and resistance to wear. They are ideal for industries where linear motion is critical‚ such as manufacturing and automotive‚ enabling efficient and reliable operation. Regular maintenance‚ like lubrication‚ is essential to extend their lifespan and ensure optimal functionality. Their versatility and precision make them a cornerstone in modern mechanical systems.
2.2 Spherical Guide Bearings
Spherical guide bearings are specialized components that accommodate angular or axial motion‚ allowing for smooth rotation in multiple directions. Their spherical surface enables them to handle misalignment and varying loads effectively. These bearings are commonly used in applications requiring multidirectional movement‚ such as in heavy machinery‚ construction equipment‚ and industrial robots. They are designed to absorb shocks and distribute stress evenly‚ making them ideal for harsh operating conditions. Spherical guide bearings are typically made from durable materials like stainless steel or bronze‚ ensuring long-term reliability. They are particularly useful in scenarios where precise alignment is challenging‚ providing flexibility and stability. Their ability to handle complex motion makes them a critical component in various industrial settings‚ enhancing overall system performance and durability.
2.3 Cylindrical Guide Bearings
Cylindrical guide bearings are designed to support linear motion and provide smooth movement along a straight path. Their cylindrical shape allows for consistent contact with the guiding surface‚ ensuring minimal friction and wear. These bearings are often used in applications requiring precise linear movement‚ such as in machine tools‚ conveyor systems‚ and material handling equipment. They are typically made from materials like bronze‚ plastic‚ or self-lubricating composites‚ which offer excellent durability and low maintenance. Cylindrical guide bearings are ideal for heavy-duty applications where high load-carrying capacity and consistent performance are critical. Their simple design makes them easy to install and maintain‚ while their self-aligning properties help absorb minor misalignments. Regular lubrication is essential to extend their lifespan and ensure optimal functionality. These bearings are widely used across industries for their reliability and ability to handle repetitive motion effectively.
Materials and Manufacturing
Guide bearings are typically made from durable materials like bronze‚ plastic‚ and self-lubricating composites. Advanced manufacturing processes ensure precise engineering for optimal performance and longevity in various applications.
3.1 Common Materials Used
Guide bearings are fabricated from a variety of materials to suit different operational demands. Bronze is widely used for its strength and resistance to wear. Plastic bearings‚ including nylon and polyethylene‚ offer excellent corrosion resistance and are ideal for lightweight applications. Self-lubricating composites‚ such as PTFE-filled materials‚ reduce maintenance needs by eliminating the requirement for external lubrication. Stainless steel and ceramic bearings are employed in high-temperature and corrosive environments‚ providing exceptional durability. The choice of material depends on factors such as load capacity‚ operating temperature‚ and the need for lubrication. Each material ensures optimal performance and longevity in specific industrial settings‚ making guide bearings versatile and reliable components in machinery.
3.2 Manufacturing Processes
The manufacturing of guide bearings involves precise processes to ensure high-quality and durability. Machining is a primary method‚ with computer-controlled lathes and milling machines shaping the materials to exact dimensions. Grinding and honing are used to achieve smooth surfaces and tight tolerances. For complex shapes‚ casting or forging may be employed‚ followed by heat treatment to enhance mechanical properties. Plastic bearings often utilize injection molding for high-volume production. Advanced techniques like surface coating or electroplating can be applied to improve wear resistance and corrosion protection. Quality control measures‚ such as dimensional inspections and material testing‚ are critical to ensuring the bearings meet industry standards. These processes collectively ensure that guide bearings deliver reliable performance in their intended applications‚ whether in industrial machinery‚ aerospace‚ or automotive systems.
Applications Across Industries
Guide bearings are essential components widely utilized across various industries such as aerospace‚ automotive‚ and industrial machinery‚ ensuring smooth motion‚ supporting heavy loads‚ and enhancing performance in critical applications.
4.1 Aerospace Industry
Guide bearings play a critical role in the aerospace industry‚ ensuring precise movement and alignment in aircraft and spacecraft systems. They are used in landing gear‚ engine mounts‚ and control surfaces‚ where reliability and durability are paramount. In spacecraft‚ these bearings support mechanisms for satellite antennas and solar panels‚ operating in extreme temperatures and vacuum conditions. The aerospace industry demands high-performance materials and lubrication solutions to withstand these harsh environments. Guide bearings in this sector are often custom-designed to meet specific application requirements‚ ensuring minimal wear and tear over extended periods. Their failure-free operation is crucial for the safety and success of aerospace missions‚ making them a cornerstone of modern aviation and space exploration technologies. The continuous innovation in bearing design and materials has enabled the aerospace industry to achieve new heights in performance and efficiency.
4.2 Automotive Industry
In the automotive industry‚ guide bearings are integral to the smooth operation of vehicles. They are widely used in steering systems‚ suspension components‚ and engine subsystems‚ ensuring precise movement and reducing wear. Linear guide bearings‚ for instance‚ are employed in automotive manufacturing lines to facilitate the assembly of vehicle parts with high accuracy. Spherical guide bearings are commonly found in suspension systems‚ allowing for multi-directional movement while maintaining stability. The automotive sector relies heavily on these bearings to enhance vehicle performance‚ safety‚ and comfort. Durable materials and advanced lubrication techniques are essential to withstand the stresses of constant motion and varying road conditions. As automotive technology evolves‚ the demand for high-quality guide bearings continues to grow‚ driving innovation in both design and manufacturing processes to meet the industry’s stringent requirements.
4.3 Industrial Machinery
Guide bearings play a pivotal role in industrial machinery‚ ensuring smooth operation and precision in manufacturing processes. They are extensively used in heavy machinery‚ such as CNC machines‚ conveyor systems‚ and robotic arms‚ where accurate movement and load handling are critical. Linear guide bearings are particularly common in industrial settings‚ providing high rigidity and load-carrying capacity. Spherical guide bearings are also utilized to accommodate angular misalignment in industrial applications. These bearings enable machinery to function with minimal downtime‚ reducing wear and tear on moving parts. Proper installation and regular maintenance are essential to prevent premature failure and ensure optimal performance. As industrial automation advances‚ the demand for high-performance guide bearings continues to grow‚ driving innovations in both design and materials to meet the sector’s evolving needs.
Installation and Maintenance
Proper installation ensures guide bearings function smoothly‚ while regular maintenance prevents wear and tear. Cleaning‚ lubrication‚ and alignment checks are critical for optimal performance and longevity of the bearings.
5.1 Proper Installation Techniques
Proper installation of guide bearings is crucial for their functionality and longevity. Begin by ensuring the housing and shaft are clean and free from debris. Apply a thin‚ even layer of high-quality lubricant to the bearing surfaces. Align the bearing precisely with the shaft‚ avoiding any misalignment that could lead to uneven wear. Use specialized tools for pressing or sliding the bearing into place‚ ensuring it is seated correctly. For bearings with set screws‚ tighten them alternately in small increments to prevent damage. Once installed‚ perform a final alignment check and test the system under controlled conditions to ensure smooth operation. Proper torque specifications must be followed to avoid over-tightening‚ which can cause premature failure. Regular lubrication and maintenance will help sustain optimal performance over time.
5.2 Regular Maintenance Practices
Regular maintenance is essential to ensure the optimal performance and longevity of guide bearings. Start by cleaning the bearing housing and surrounding areas to remove dirt and debris‚ which can cause wear and contamination. Inspect the bearings for signs of wear‚ such as scoring or discoloration‚ and replace them if necessary. Lubrication is critical; apply the recommended type and amount of grease or oil to reduce friction and prevent overheating. Check the alignment of the bearing and shaft regularly to avoid misalignment issues. Monitor operating temperatures and vibration levels‚ as excessive heat or vibration can indicate impending failure. Schedule periodic inspections and replacements based on the manufacturer’s guidelines and the application’s workload. Proper maintenance not only extends the life of the bearings but also ensures the overall efficiency and reliability of the machinery.
Common Failure Modes
Guide bearings commonly fail due to overloading‚ causing excessive stress and wear. Misalignment‚ contamination‚ and inadequate lubrication also lead to premature failure. Regular checks are essential to prevent these issues.
6.1 Overloading
Overloading is a primary cause of guide bearing failure‚ occurring when the applied load exceeds the bearing’s rated capacity. This leads to excessive stress on the rolling elements and raceways. Prolonged overloading accelerates wear‚ causing irreversible damage. Symptoms include uneven wear patterns‚ increased operating temperatures‚ and noise. Addressing overloading requires proper load calculation and selecting bearings with appropriate load ratings. Regular monitoring and timely replacement are crucial to prevent operational disruptions and ensure machinery longevity. Proper installation and maintenance practices can mitigate risks associated with overloading‚ enhancing overall system reliability and performance. Understanding load limits is essential for optimizing bearing lifespan and maintaining efficient machinery operation.
6.2 Misalignment Issues
Misalignment is another common failure mode in guide bearings‚ occurring when the bearing axes are not properly aligned. This can result from improper installation‚ uneven surfaces‚ or operational stresses. Misalignment leads to uneven stress distribution‚ causing increased friction and heat generation. Over time‚ this accelerates wear on the bearing components‚ reducing their lifespan. Symptoms include vibration‚ noise‚ and premature wear patterns. Severe misalignment can lead to catastrophic failure‚ halting machinery operation. To mitigate misalignment‚ precise installation techniques and regular inspections are essential. Using alignment tools and ensuring proper mounting surfaces can prevent such issues. Addressing misalignment early is critical to maintaining bearing performance‚ reducing downtime‚ and extending equipment longevity. Proper maintenance practices‚ such as checking alignment during routine inspections‚ are vital for preventing misalignment-related failures.
Advantages of Guide Bearings
Guide bearings offer enhanced precision‚ increased equipment longevity‚ and reduced operational costs. They ensure smooth motion‚ minimize wear‚ and optimize performance across various industrial applications‚ making them indispensable for modern machinery.
7.1 Enhanced Precision
Guide bearings significantly enhance precision by ensuring accurate alignment and smooth movement in mechanical systems. This is particularly crucial in industries requiring high tolerances‚ such as aerospace and precision manufacturing; By minimizing deviations and vibrations‚ guide bearings allow for consistent and reliable operation. Their ability to maintain exact positional control reduces errors and improves the overall quality of output. In applications like CNC machines and robotic systems‚ this level of precision is essential for achieving desired results. Enhanced precision also leads to reduced waste and increased efficiency‚ making guide bearings a vital component in modern industrial setups.
7.2 Increased Equipment Longevity
Guide bearings play a crucial role in extending the lifespan of industrial equipment by minimizing wear and tear. By providing smooth motion control and reducing friction‚ they prevent excessive stress on moving parts. This leads to fewer mechanical failures and a significant reduction in maintenance needs. Additionally‚ guide bearings help distribute loads evenly‚ avoiding concentrating stress in specific areas. This uniform load distribution ensures that machinery operates within safe limits‚ thereby prolonging its operational life. In industries like manufacturing and heavy machinery‚ where equipment is subjected to constant use‚ guide bearings are essential for maintaining durability. Their ability to protect against premature wear directly translates to cost savings through reduced repair and replacement costs. By ensuring equipment longevity‚ guide bearings contribute to overall operational efficiency and productivity.
Future Trends
Advancements in materials and technology are driving the evolution of guide bearings‚ with a focus on smarter designs and improved durability to meet future industrial demands efficiently.
8.1 Technological Innovations
Technological advancements are revolutionizing guide bearings‚ with innovations like smart bearings embedded with sensors for real-time monitoring. These sensors detect wear‚ temperature‚ and lubrication levels‚ enabling predictive maintenance. Integration with IoT allows seamless data transfer‚ optimizing performance and reducing downtime. Self-lubricating materials and nano-coatings are being developed to enhance durability and reduce friction. Additionally‚ modular designs are emerging‚ offering customization and easier replacement. These advancements aim to improve efficiency‚ reduce costs‚ and extend the lifespan of machinery in various industries. The focus is on creating intelligent‚ adaptive bearings that can thrive in demanding environments while minimizing environmental impact. Such innovations are set to redefine the role of guide bearings in modern machinery.
8.2 Material Advancements
Material advancements in guide bearings are driving improvements in durability and performance. High-performance polymers and advanced alloys are being developed to withstand extreme temperatures and corrosive environments. Lightweight yet robust materials‚ such as carbon fiber-reinforced polymers‚ are reducing weight while maintaining strength. Self-lubricating materials and coatings are minimizing friction and wear‚ extending bearing life. Additionally‚ researchers are focusing on eco-friendly materials‚ such as lead-free alloys‚ to align with global sustainability goals. These innovations are enabling guide bearings to operate efficiently in harsh conditions‚ from industrial machinery to aerospace applications. The integration of nanotechnology and advanced surface treatments further enhances wear resistance and load-carrying capacity. As materials science evolves‚ guide bearings are becoming more reliable‚ adaptable‚ and environmentally responsible‚ meeting the demands of modern industries while reducing maintenance and operational costs.
Guide bearings play a vital role in mechanical systems‚ ensuring alignment and reducing friction. Their diverse types and materials cater to various applications‚ enhancing efficiency and longevity across industries.
9.1 Summary of Key Points
Guide bearings are critical components in machinery‚ ensuring precise alignment and reducing friction. They come in various types‚ including linear‚ spherical‚ and cylindrical‚ each suited for specific applications. Proper installation and maintenance are vital for longevity and efficiency. Common materials like steel and bronze offer durability‚ while advanced manufacturing processes enhance performance. Across industries‚ guide bearings are essential for smooth operation‚ from aerospace to automotive and industrial machinery. They prevent wear‚ enhance precision‚ and extend equipment life. However‚ issues like overloading and misalignment can lead to failures. Regular maintenance practices‚ such as lubrication and inspection‚ are crucial to mitigate these risks. Technological innovations and material advancements promise even greater efficiency and reliability in the future. Understanding these aspects ensures optimal use of guide bearings in modern machinery.
9.2 Final Thoughts
Guide bearings are indispensable in modern machinery‚ offering precision‚ stability‚ and durability. Their ability to minimize friction and wear makes them a cornerstone of industrial efficiency. While they require careful installation and maintenance‚ their benefits far outweigh the challenges. As technology evolves‚ advancements in materials and design promise even greater performance and reliability. Embracing these innovations will be key to unlocking future potential. Ultimately‚ guide bearings remain a vital component in ensuring the smooth operation of machinery across diverse industries‚ underscoring their enduring importance in mechanical systems.